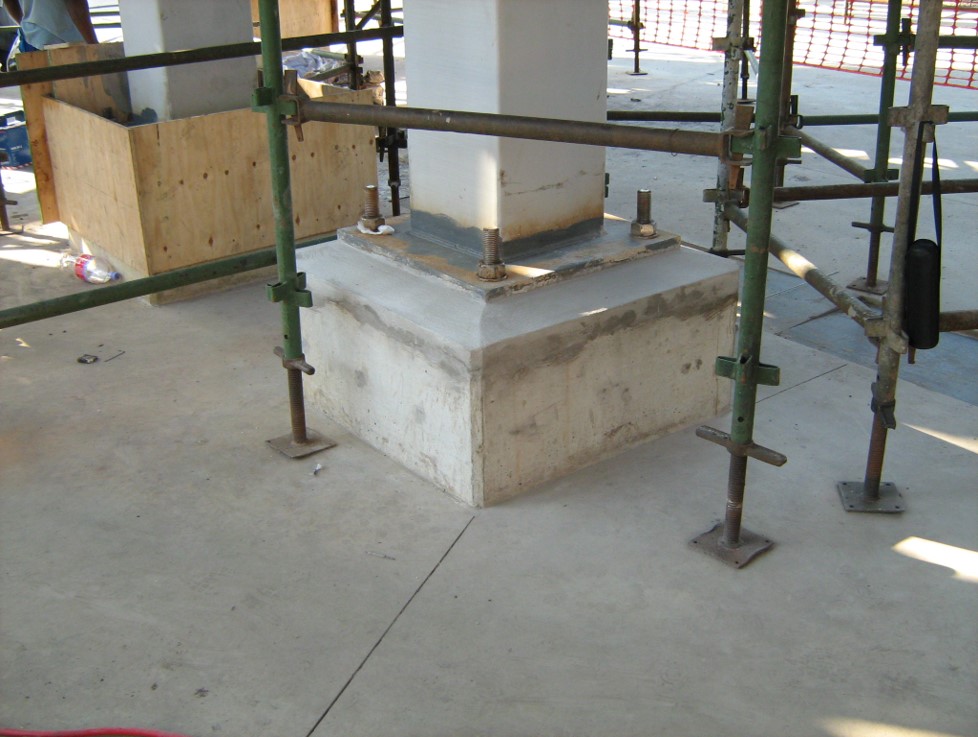
The American Concrete Institute cover all things grouting in their comprehensive report - ACI 351.1R-99: “Grouting between Foundations and Bases for Support of Equipment and Machinery.”
According to the American Concrete Institute: “The most important requirement for a grout that is intended to transfer loads to a foundation is that it has volume change characteristics that result in complete and permanent filling of the space.”
A true non-shrink grout will not exhibit shrinkage in either the plastic, or hardened state of the curing process and will support the plant, or equipment being grouted for the life of that plant, or equipment.
The term “non-shrink” grout is one that is used widely but often not clearly understood or defined. It is not uncommon for commercially available “non-shrink” grouts to exhibit shrinkage when tested by the relevant test methods. Because of this, it’s important that engineers, specifiers and owners understand the important role that the grout plays and that although an important performance property, Compressive Strength is not the most important performance property of a grout. That title belongs to the grouts non-shrink properties.
Any grout specification should therefore start by specifying exact performance properties with respect to vertical height change characteristics of the grout. The generic use of the term non-shrink in grouting specifications is insufficient. It’s equally important that contractors understand this critical performance property. A successful grout job is the joint responsibility of the engineer, the contractor, and the manufacturer.
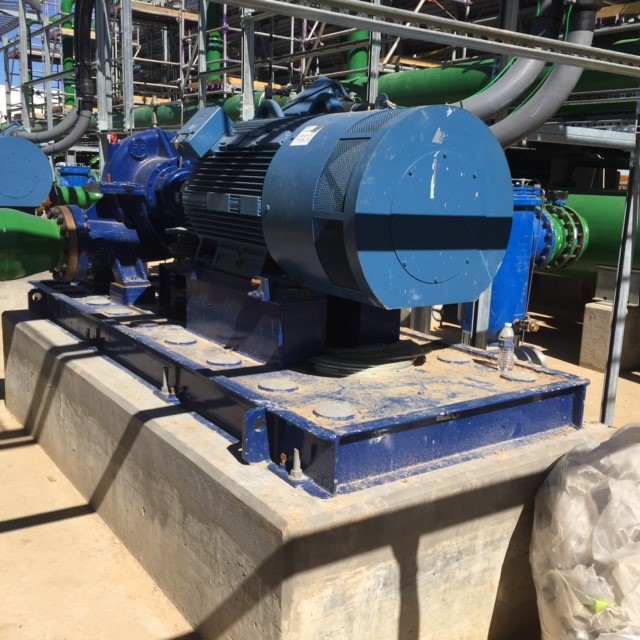
Selecting the right non-shrink grout:
The proper selection and specification of non-shrink grout is extremely important When selecting a grout, as a starting point it is important to understand the type of load that the grout will be subjected to. It’s equally important to give due consideration to the parameters of the application in question. Questions to ask could include:
- What is the clearance between foundation and base plate?
- What are the dimensions to be grouted i.e. what volume of grout needs to be placed?
- What consistency is required to place the material efficiently?
- What is the working time of the grout?
- What are the service temperatures that the grout will be exposed to?
- What are the expected temperatures in which the grout will be installed?
- Are there special considerations? i.e. Underwater applications, aggressive chemical exposure, electrical resistivity considerations, etcetera …
Non-shrink cementitious grouts are designed for static or light dynamic loading and are preferable for applications subject to high temperature exposure.
Unless shown otherwise on Engineering Drawings, non-shrink cementitious grout would typically be used for:
- Grouting of Structural Steel elements
- Column Base Plates
- Equipment on cast bases
- Joints in pre-cast concrete
- Rotating equipment, motors, drives and pumps under 150 kW (200 hp) as a rule of thumb
Sometimes however, an epoxy grout is required. Non-shrink epoxy grouts are higher priced than cementitious grouts but offer significantly better performance properties and are designed for heavy dynamic loading from vibration or impact. They are also best suited for applications requiring good chemical resistance.
Unless shown otherwise on Engineering Drawings, epoxy grout would typically be used for:
- Rotating equipment, motors, drives and pumps over 150 kW (200 hp) as a rule of thumb
- Compressors, generators and turbines
- Crane Rails
- All sole plate mounted equipment
- Grout subject to chemical attack
Most leading grout suppliers offer detailed grout selection charts for reference and these are an invaluable tool in ensuring that the correct grout is selected.
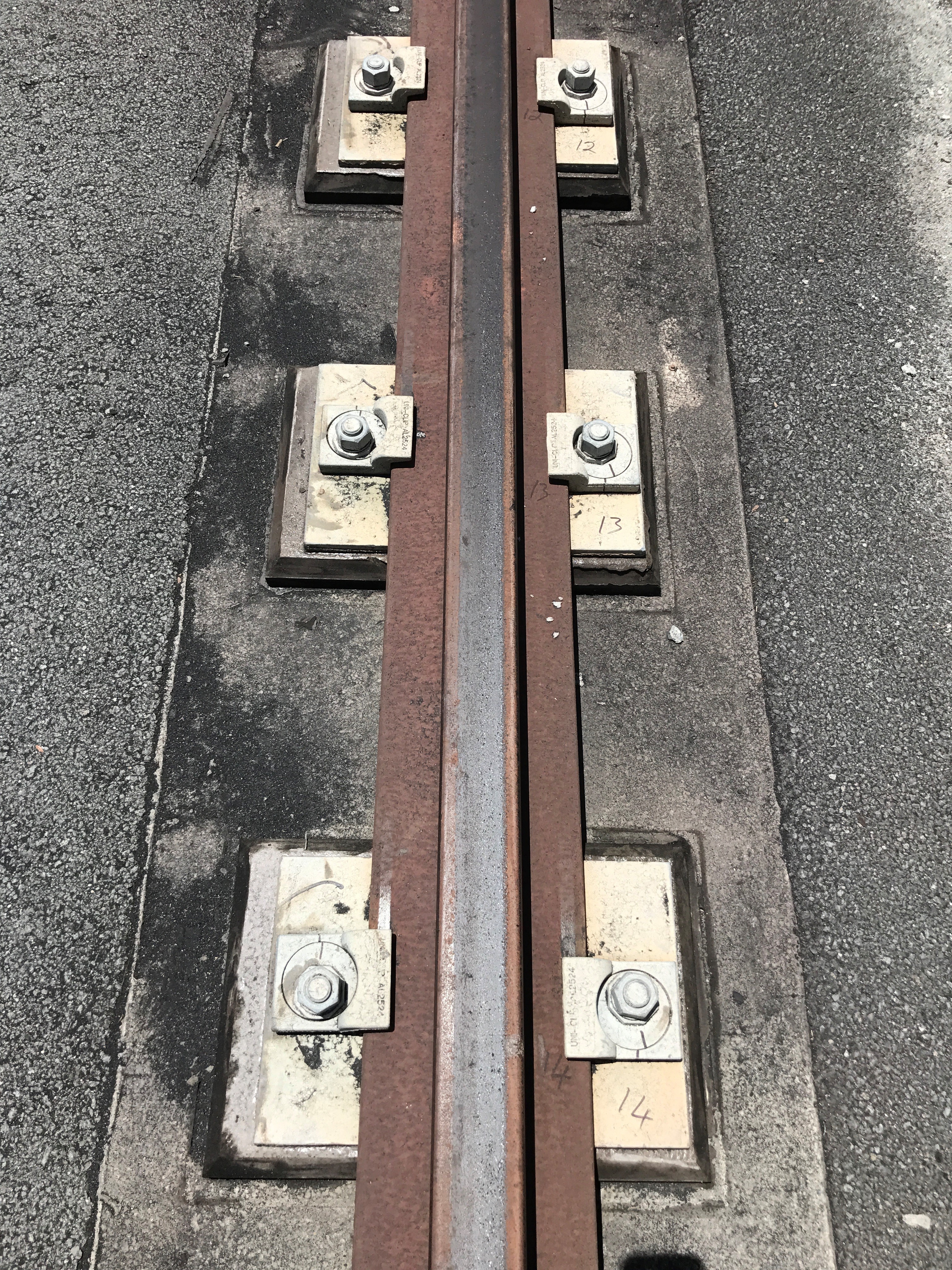
Conclusion:
When selecting a grout to be used as load-transfer material between machine and equipment base plates and their foundations, or the filling of the spaces between load-carrying members, such as under column baseplates or in precast concrete joints, there are many important material performance properties and situational factors to be considered in selecting the right material, but the vertical height change properties of that material should be considered as the most important criteria in making that decision.
To find out more about our range of Euclid Chemical industrial grouting solutions visit https://www.tremco.com.au/products/concrete-masonry-products/grouts or contact our National BDM Grouts & Repairs, Simon Ross to discuss your specific project requirements.